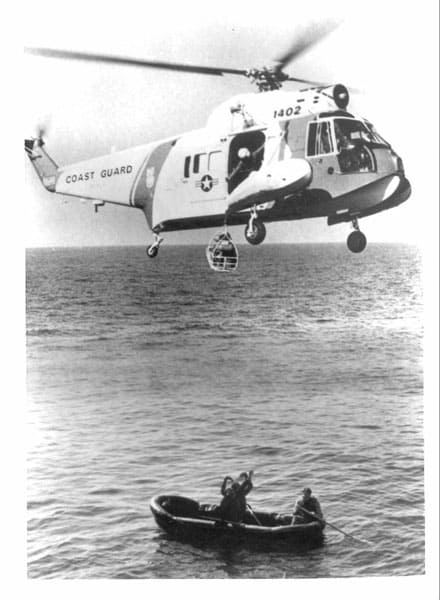
The Coast Guard Aviation Plan of 1957 called for 79 medium range helicopters capable of proceeding offshore at a reasonable speed to a distance of 300 nautical miles, hovering for 20 minutes while picking up at least six survivors and then returning to base with a fuel reserve equal to 10% of the initial fuel load. The Board preferred a multi- engined turbine powered aircraft. Those available were larger in size than envisioned, in limited production at the time, and expensive. The Sikorsky HUS (H-34), a piston engine powered helicopter, met operational requirements and was selected for purchase. Three P5Ms, 14 UFs and six C-130Bs purchased as part of the plan resulted in a limited purchase of only six HUS due to budgetary limitations. Three of the original six crashed while in a hover, two of unknown causes, and in 1962 the Coast Guard was looking for a different helicopter to meet requirements.
Options were limited. Sikorsky had designed, a single engine, turbine powered, amphibious helicopter designated the S-62. The S-62 had been designed for the commercial market but was not purchased in great numbers. The engine was deemed too big and expensive and passenger carrying capability was limited. None of the other military branches were interested in it either. The Army was having problems with the HU-1 Huey at the time but was completely committed to the program. The Navy was committed to the Kaman H-2 and was having problems with it also. The Air Force was not particularly interested in helicopters at this time.
The S–62 however, had features that were desired by the Coast Guard. It floated on an amphibious hull, it had turbine power, had a large main cabin and it was built utilizing proven components. The automatic stabilization system used on the S-62 was a scaled version of the larger S-61 (SH-3). The rotor system came from the S-55 (HO4S), as did most of the drive system which had already proven to be reliable. The assembly was design limited to 730 shaft horsepower. Small jet engines suitable for helicopters were rare and not available at the time. Sikorsky solved the problem by using a 1230 SHP General Electric T-58-GE-8B engine and derating it. With the extra 500 HP worth of air capacity on the front end density altitude was not an operational problem.
The Coast Guard needed a helicopter and Sikorsky needed to sell the S-62. Unlike Department of Defense agencies, the Coast Guard could buy a non milspec aircraft. Sikorsky approached the Coast Guard and offered the S-62. Previous problems with the HUS created hesitancy on the part of the Coast Guard resulting in Sikorsky Aircraft agreeing to test the S-62 at the manufacturer’s expense.
The Navy test facilities at Patuxent River Maryland were utilized and LCDR Frank Shelly USCG, a graduate of the Navy Test Pilot School, was assigned to the project as test pilot and program coordinator. Shelly worked closely with Sikorsky Aircraft in the initial and test phases of the HH-52. He designed and set up the test program. It consisted of Coast Guard operational requirements, the verification of Sikorsky’s performance claims, and anticipated maintenance requirements. During the many hours of flight testing the “by the numbers” autorotation and the “beep to hover” procedures were developed. The “beep to hover” meant the completion of countless night over water missions and the safety of many HH-52 crews. The helicopter performed well and the Coast Guard signed on.
Originally designated the HU2S-1G it became the HH-52A. It had a rotor diameter of 53 feet, a range of 474 miles and a top speed of 109 mph. It was an extremely flexible rescue aircraft that could fully perform missions with a minimum crew. It was well suited for night and all-weather flight. The HH-52 had a hydraulic hoist and carried a rescue basket. The cabin could accommodate up to ten passengers or six litters. It was fully amphibious and was equipped with a removable foldout rescue platform that looked like a large extended step. It was a rectangular grid that sloped slightly downward beneath the water’s surface when the helicopter was afloat. Incapacitated survivors could be scooped or dragged onto it greatly facilitating their rescue.
On January 9, 1963 the U.S. Coast Guard received the first of 99 Sikorsky S-62’s which were given the designation HH-52A and the name “Seaguard”, a name which never caught on amongst those who flew it. The HH-52 was the Coast Guard’s first amphibious, turbine-powered helicopter.
The HH-52, with over 15,000 lives saved in its twenty-six years of service, has the honor of having rescued more persons than any other helicopter in the world. This little helicopter, a unique assemblage of proven parts, comfortably behind the cutting edge, performed astounding feats in thousands upon thousands of occasions. It became the international icon for rescue and proved the worth of the helicopter many times over. It had an enormous impact on Coast Guard aviation.
Beep to Hover
The following is an abbreviated version of then LCDR Frank Shelly’s commentary on the development of the Beep to hover maneuver. Shelley was the HH-52A project test pilot. He was ably assisted by ADCM Clayton Roll.
A helicopter approach to landing is contrary to everything taught for a fixed wing Stabilized Approach wherein the same speed over the final approach point is maintained to a half mile out and continued until the round out over the runway. The helicopter, on the other hand, wants to go from cruising speed at altitude to zero speed four feet above the landing spot. This means that the helicopter is decelerating and descending at the same time on approach. During daylight VFR operations the pilot is able to observe visual reference indications that make the maneuver easier than it sounds. Close in adjustments are within the capability of the helicopter. Instrument flight or night over water operations (essentially instrument flight) is something else. That was why the artificial stability systems with an auto hover feature in the HUS generation of helicopters were so welcome. The pilot, however still had to monitor rotor/engine RPM.
Constant RPM in flight is of extreme importance. There are two reasons for this, one is structural and the other is power related. We cannot make the rotor constant speed like an aircraft propeller because rotor pitch angle is related to the angle of attack resulting in a constant messing with the lift. Instead a change in torque must be provided by a governor working directly on the engine. The governors available at the time were not sensitive enough to keep a piston engine at constant RPM with varying torque demands. Enter the free turbine jet engine such as the one in the HH-52A. With the engine power turbine spinning up at 27,000 to 30,000 RPM a one percent change could be easily sensed by the governors available at the time. They could then be used to adjust the fuel control to increase/decrease the fuel input which increased/ decreased the temperature which either spun up or down the compressor giving an increase/decrease of flow through the power turbine. Thus the pilot could set the desired RPM and not have to monitor it.
There is an additional aerodynamic feature that enters into the equation. When a helicopter rotor system is in a hover, the lift is generated solely by the airflow from rotation. However the plane of rotation equates to a disc and if this disc translates in any direction so as to generate airflow of more than six knots across the disc, an additional lift is generated. The faster the disc is moved in any direction, the more “translational lift” is produced. At cruising speed, it is a significant portion of the lift holding the helicopter up. If the rotor disc is tilted slightly back during cruise you lose some of the forward thrust vector and the helicopter slows and as a result you lose some of the translational lift. The turbine governor keeps the rotor turning at the same speed and the rotational part of the lift remains constant. You do however have a decrease in overall lift and the helicopter starts to descend.
During the evaluation and test of the HH-52 numerous transitions to hover were made during which altitude/airspeed check points were recorded as the maneuver progressed. Armed with this information Shelly and Roll reasoned that just putting a little “beep” of back trim on the electric trim button in level flight would start the deceleration/descent. (It could be accompanied by a small initial power reduction) Then as each check point “window” was reached, feeding in another “beep” kept the maneuver going. It was a pretty much hands off, feet on the floor with maybe an extra withheld “beep” or a power tweak to hit each window.
To use this maneuver to investigate something on the water at night, the pilot would fly over the object on a downwind heading proceeding outbound for a couple of minutes while descending to the initial radar altimeter altitude. A procedure turn, similar to a no vector, non-precision instrument approach, was used to bring the helicopter back into the wind where a final approach was started. With any reasonable weather conditions, whatever it was that you wanted to look at was in front of you when you got to a 20 foot radar altitude and zero airspeed. The same procedure was utilized in areas of reduced visibility. The Mobile training center later taught a teardrop pattern to save time but the principle remained the same.
With a modern electronics suite and automatic flight control systems this procedure is both primitive and not necessary. At the time, however, it greatly expanded the operational capabilities of the aircraft and resulted in the rescue and saving of lives that otherwise would not have been possible.